ニキシー管作品制作記 No.8
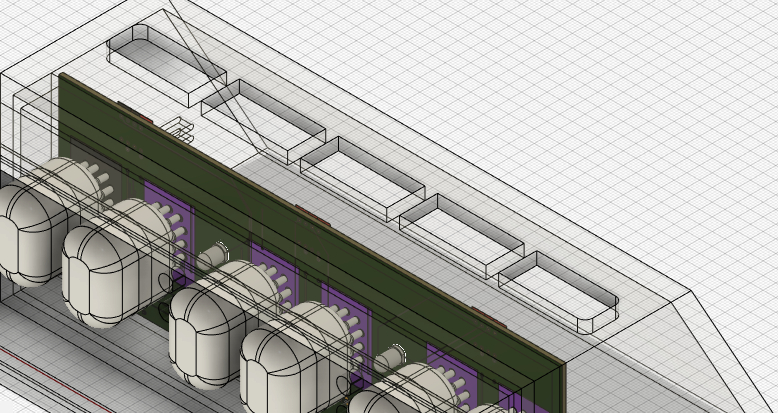

2023年10月30日
前回のあらすじ
筐体のミスが発覚した。
Autodesk Fuision 360 -再構築-
筐体の大きさ一部が間違っていたため、修正が必要になった。操作を覚えたので全部最初からやろうかとも思ったが、流石に面倒過ぎたのであるものを修正する方向にした。
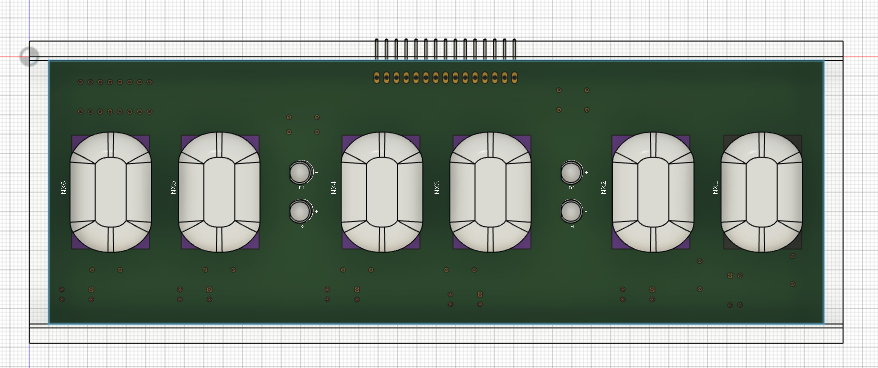
フットプリントも合わせて直した。再構築終わり。
Autodesk Fuision 360 -フットプリントを完成させる-
ニキシー管とLEDの配置ができたので、他の部品の配置を綺麗にしていこう。
ピンヘッダは中央に配置したい。これの中心点は横200mmの基板から見ると100mm地点に配置できる。
ここからはインチの出番だ。
グリッドの設定を0.01 inchや0.1 inchに変えて配置を行う。
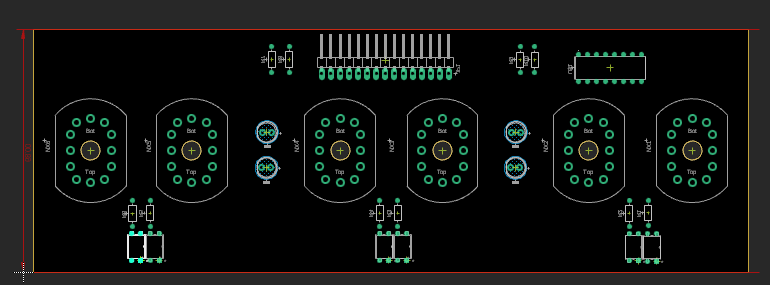
ここから配線だ。まずは複雑なニキシー管間の連結を行う。
自動配線もできそうだが、めちゃくちゃになりそうなので手動配線をする。
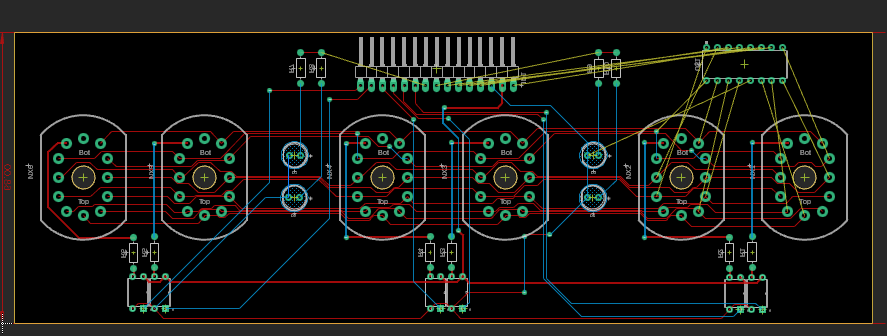
ニキシー管・LED・フォトカプラを繋いだ。半自動配線のような感触で結構悪くない。
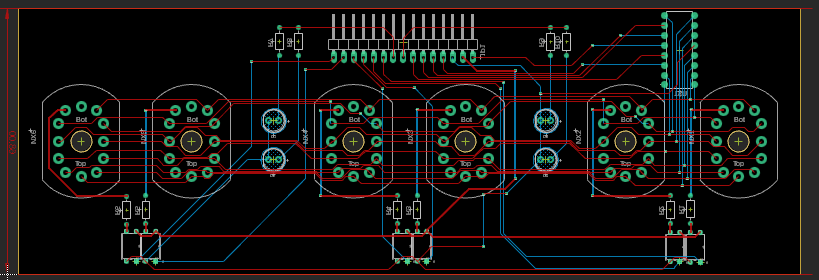
全部配線し終わった。3Dにプッシュして見てみよう。
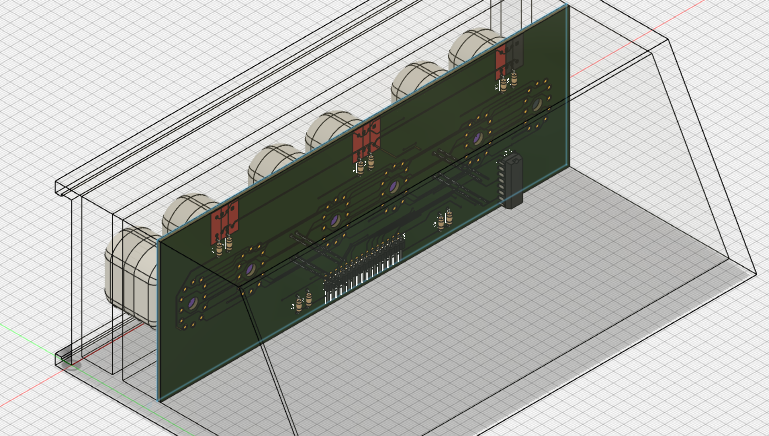
大丈夫そうだ。では、次の問題に移ろう。
リバースエンジニアリングタイム -最初の確認-
物理的なタクトスイッチを隠しつつ、どのような配置をすれば既に出回っているような製品のボタンを作れるのか?
筐体を繋ぎ合わせるための機構もどう作ればいいのかわからない。
やろうとしていることが完全に専門外で何一つ分からないのだ。
こういう時は既にあるものを解体して見てみるのが一番だ。こういう行為をリバースエンジニアリングという。
しかし、リバースエンジニアリングというのは場合によっては違法性がある。特にプログラム等は禁止されている例をよく見かける。
人気ドラマ「下町ロケット」でもリバースエンジニアリングを行っていたが、構造の特許問題でひと悶着あったと思う。
私は日本を代表する企業の機械を分解しようとしている。これの内部を無断で公開することはかなり問題がある。ここからは画像をあまり添付せずに内部構造に言及する。
ということで、リバースエンジニアリングタイム。
まずは既に手元にあるのに
リバースエンジニアリングタイム -Entry No.1-
Nintendo DS。さて、ABXY, 十字キー, LR, START, SELECTキーはどうなっているのか?
機械的に反応する部分のボタンが平たい(よくあるタクトスイッチではない)。それに密度が高いのでガバガバになったりもしない。LRボタンなどは構造が結構複雑だ。
平たいボタンを覆うようなゴム製のシートっぽいものがある。
十字キーという概念はいつ見ても素晴らしい発明だ。LRボタンはボタン以外の機械的に複雑なパーツも多い。
リバースエンジニアリングタイム -Entry No.2-
ガチャガチャの「日本信号 ミニチュア灯器コレクション 車道編」 より 歩行者用押しボタン箱
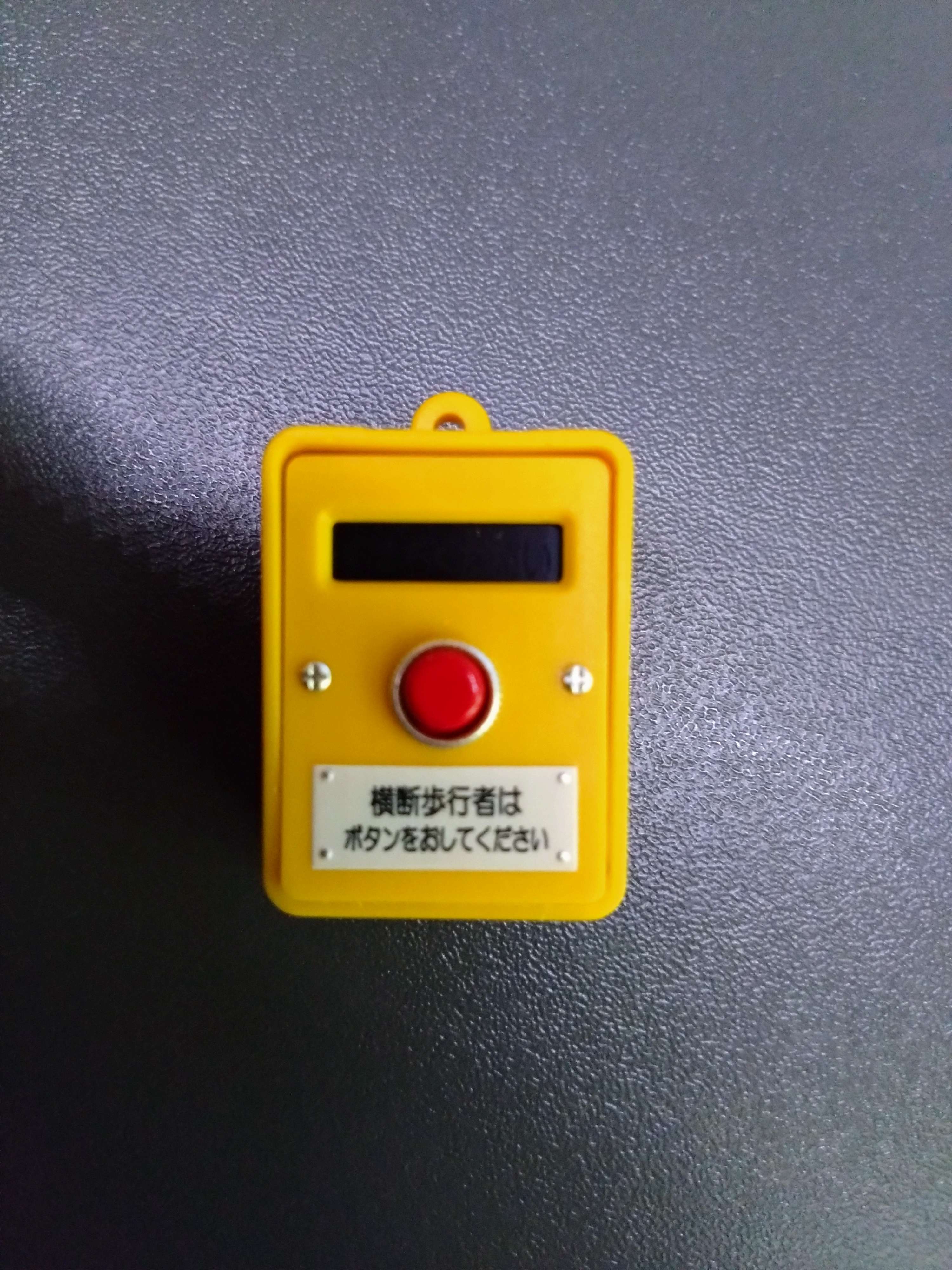
単純な回路とは言え、このクオリティを300円で出せているガチャガチャという商業は一体どうなっているのだろうか。
正直三倍の値段でも私なら買う気がする。っと、感想を述べる場ではない。構造を研究するのだ。
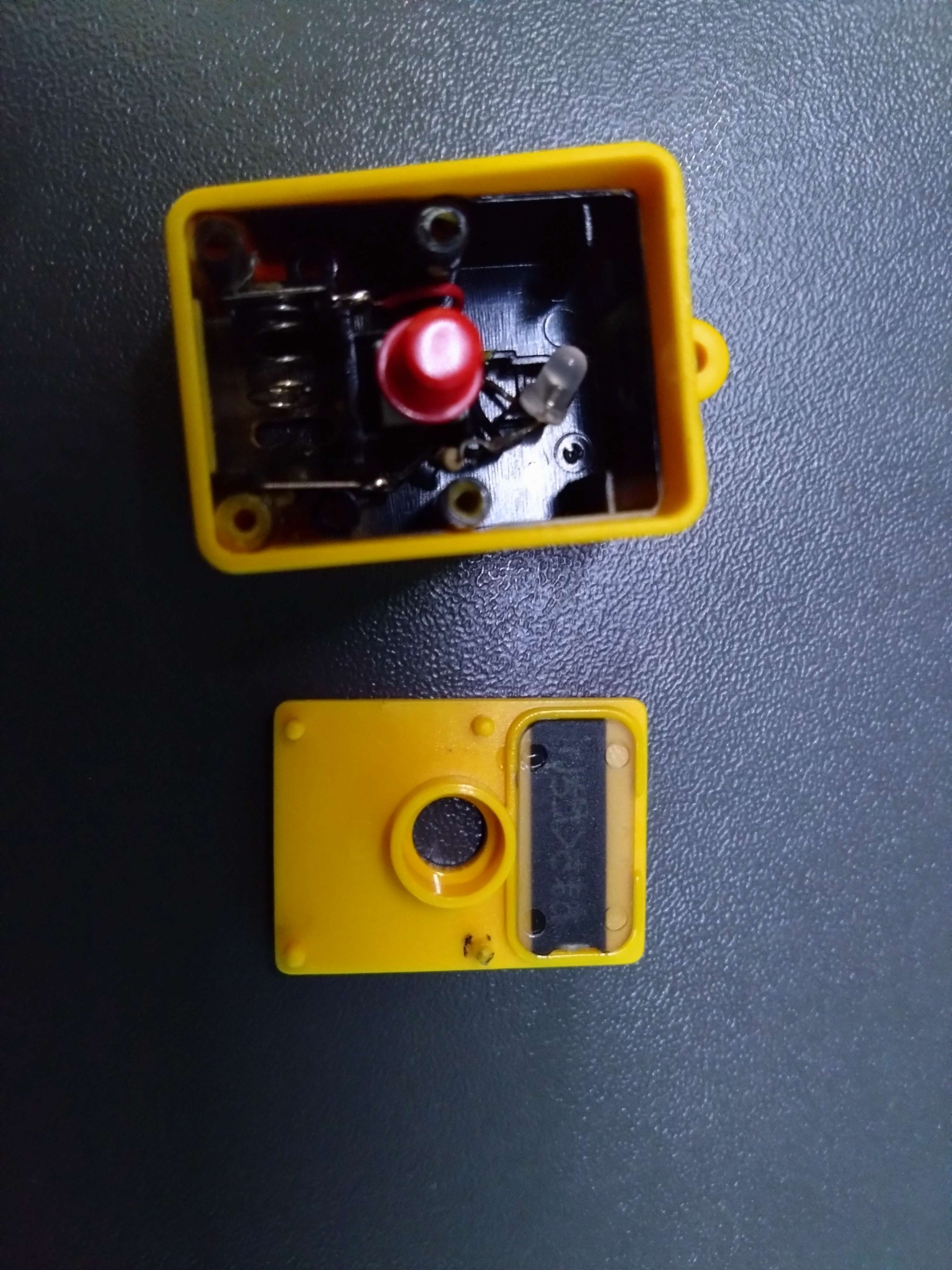
中身はこう。ボタンは結構安定していない。それと一度閉めると開けるのが結構難しい。
すなわちパーツがピッタリハマっている。この商品はこの機構で安定性と費用を確保していることを意味する。設計が(いい意味で)簡素なのだ。
3Dプリンタではこのクオリティを出すことは出来ないのではなかろうか。というかピッタリハマってなかなか抜けないのは困る。
リバースエンジニアリングタイム -Entry No.3-
そこらへんにあったエアコンのリモコン
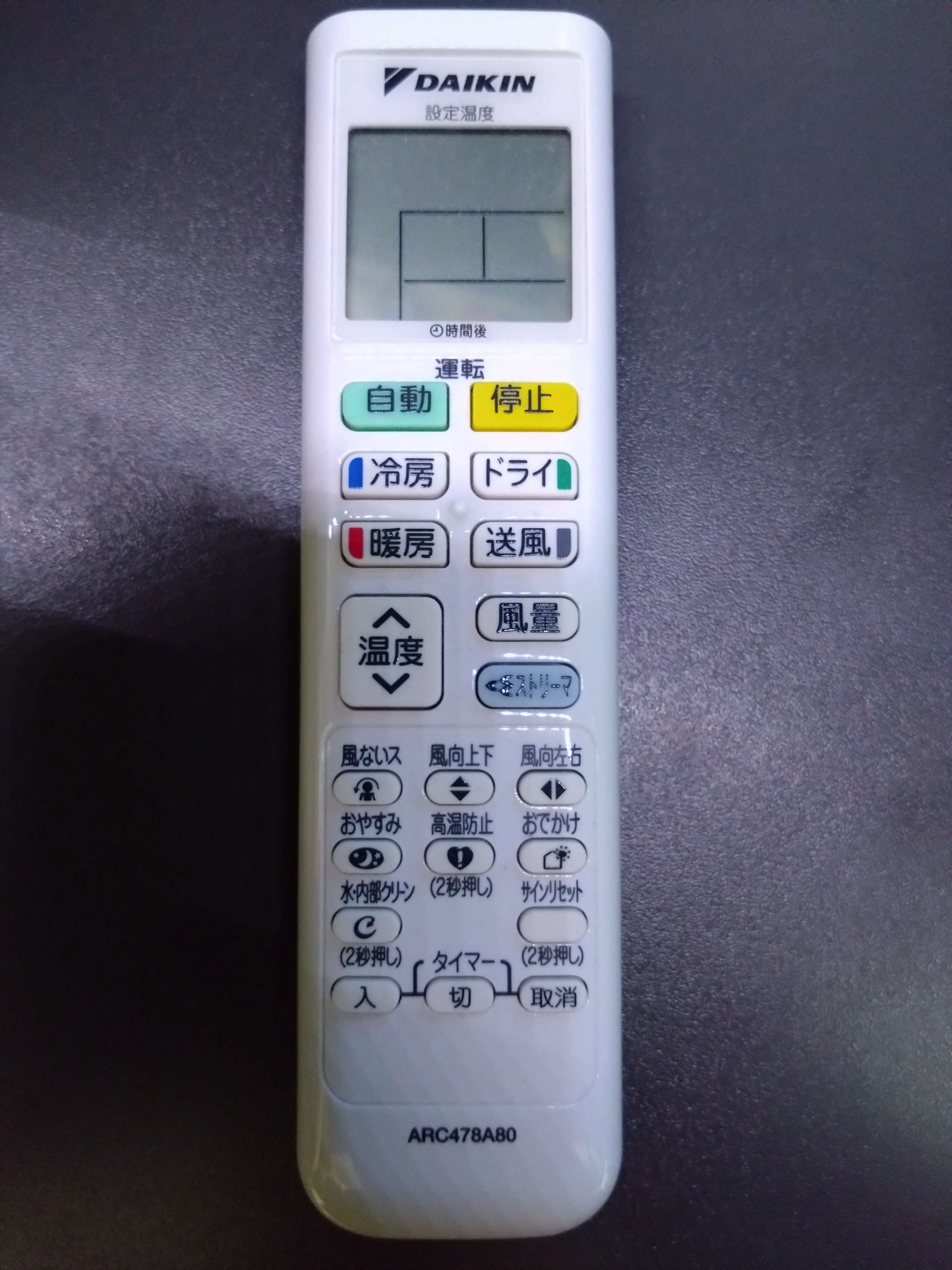
このリモコンで参考になるのが「スライド式の蓋」だ。
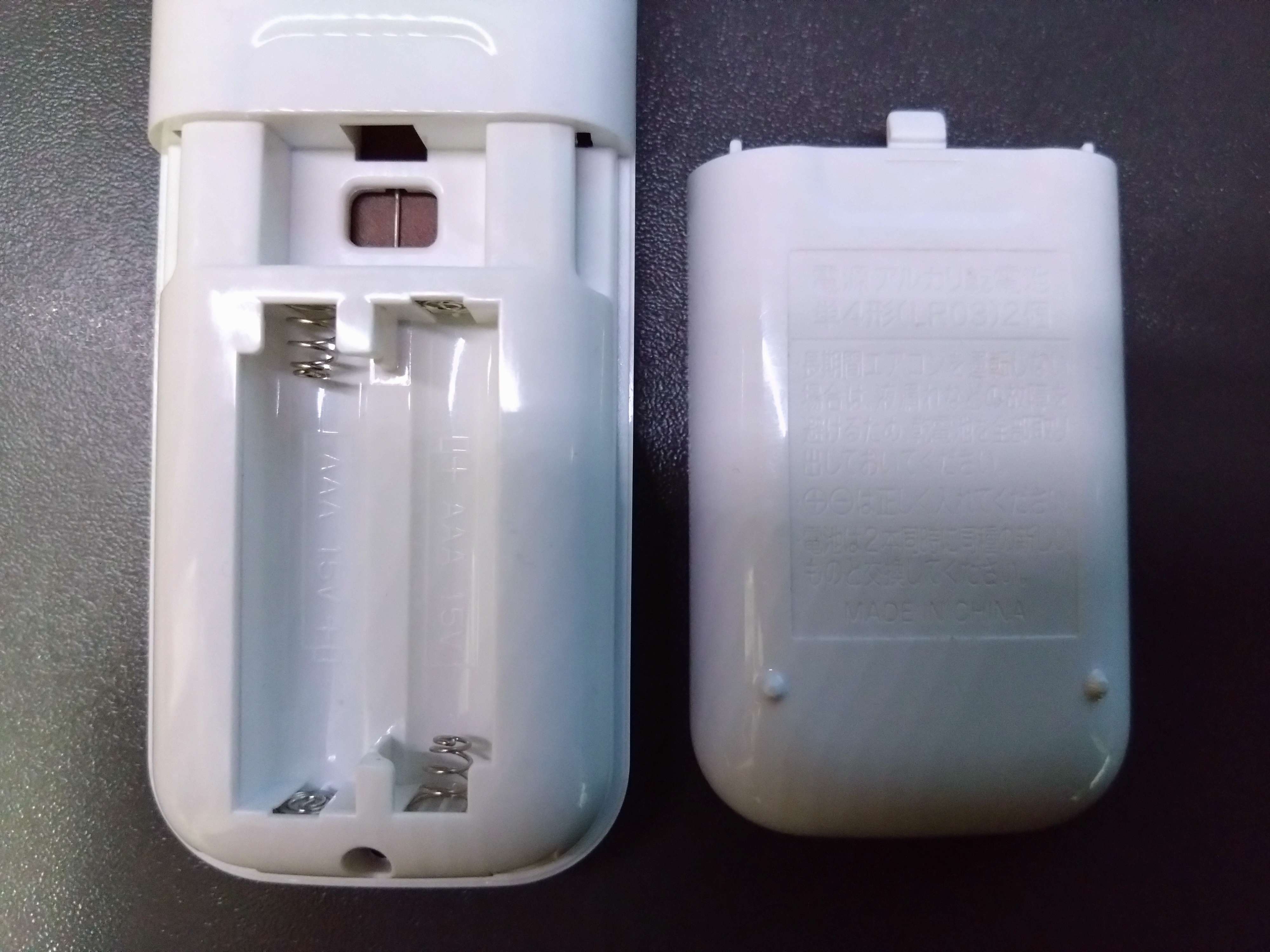
この部分だ。普段気にしていない何気ない部分にもこういう機構は五万と存在している。
少し押し込んでフックを外し、スライドして蓋を外す。何気ないが、ここだけでも人間の技術の発展を垣間見ることができる。
さらに分解したかったが、力技になって破壊しそうだったのでやめた。十分収穫はあった。
リバースエンジニアリングタイム -Entry No.4-
本丸、TOSIBAの色々機能が入ってるCDラジオ(CDプレーヤ・ラジオ・目覚まし時計)
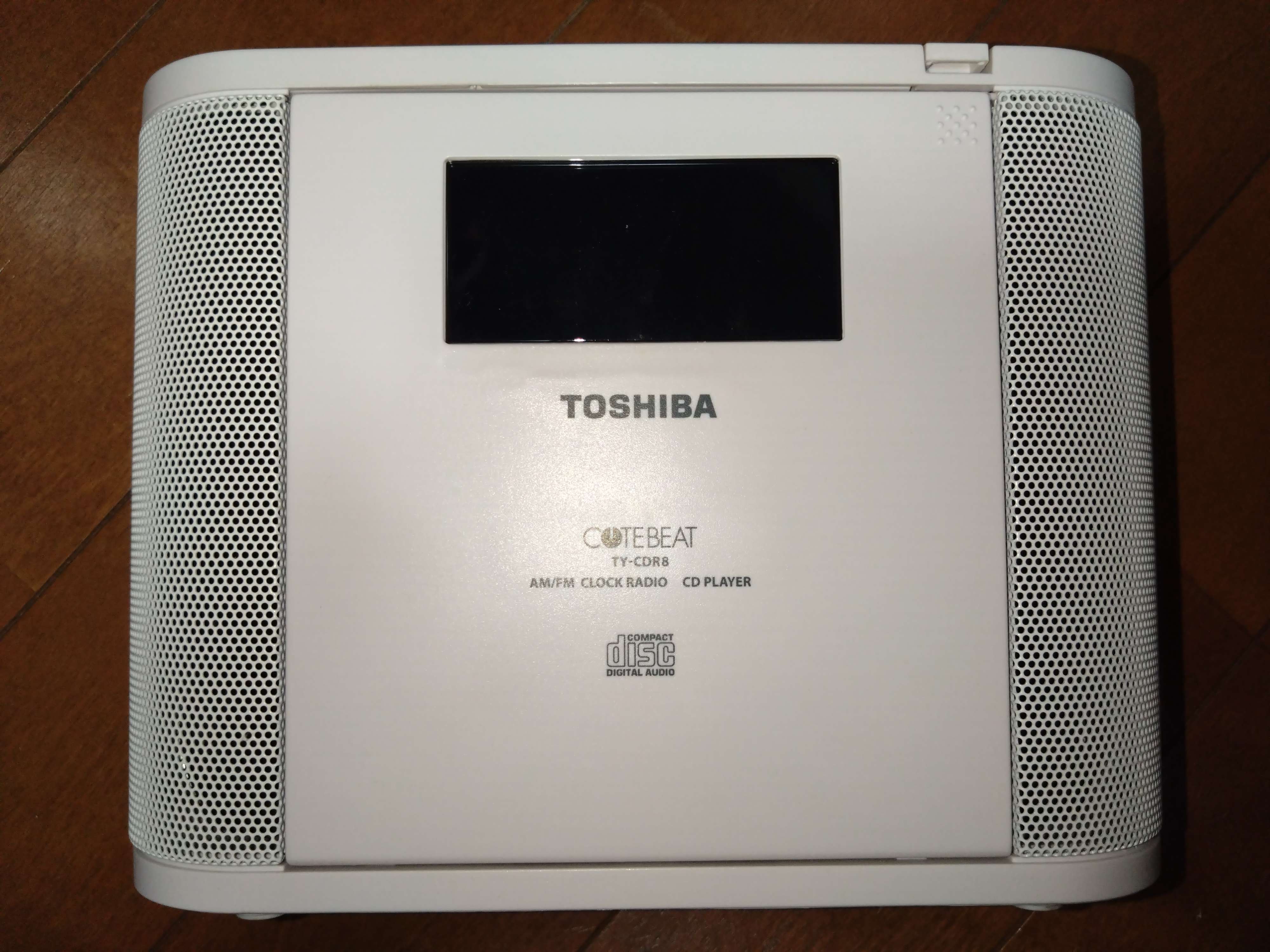
20分程かけて、蓋を取り外すことができた。素晴らしい機構をしている。産業技術の宝庫がそこにはあった。
まず、配線の外し方が分かるようになった自分の成長度に感動した。不可逆な破壊を起こさずに中身を見ることができたのだ。
しかも、各主要部品が何者なのかおおよそ分かる。
外部からの入力はこれもタクトスイッチを利用している。基板の固定方法は非常に参考になる。
何故スイッチの回路がこうなっているのか今の私ならわかる!凄い!この構造なら確かに簡略化できる!
リボンケーブルの扱いにやきもきしながら機械を組みなおした。
リバースエンジニアリング -結果-
タクトスイッチ + カバーという方式ができるなら、それがよさそうだ。勿論、基板を余計に作る必要がある上に、ねじ止めの機構が必要そうだ。
そして一つ、3Dプリンタでは確実に再現できないであろう機構がある。
ねじ穴だ。3Dプリンタの印刷精度では産業機器に匹敵するねじ穴は十中八九作れない。
ではこれをどうやって設計する?
それも考えつつ、最初の筐体に戻って設計を変更しよう。
Autodesk Fusion 360 -筐体改造-
そもそも現状の筐体には色々問題がある。ボタンの配置はもとい、基板を入れる方法、電源を供給する方法、といったところだ。
筐体の中身を考慮して、ボタンの配置場所を決める。イメージ図はどうなっていたか。
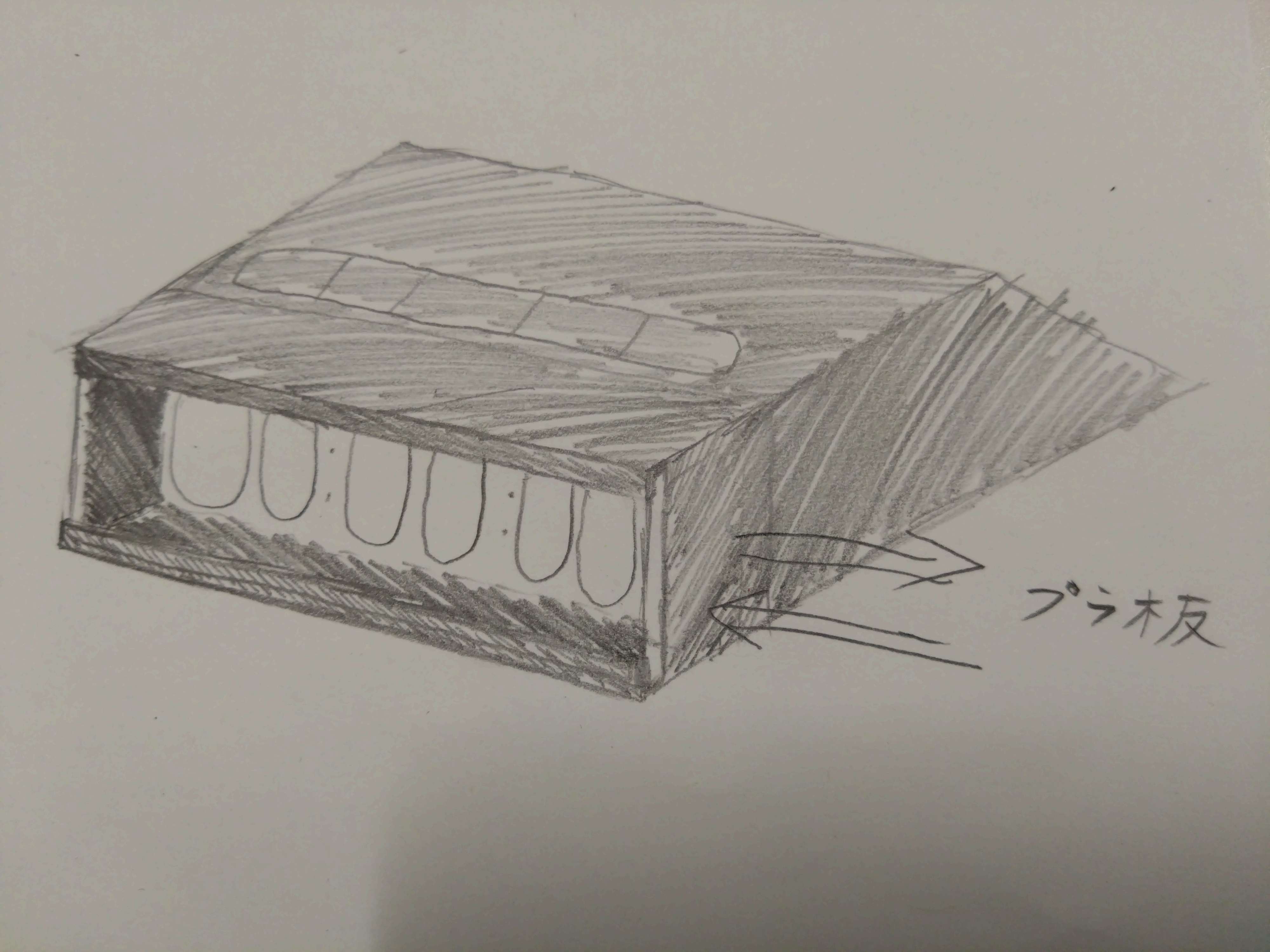
ボタンは結構手前に出ている。これの通りに作るとなると、先程作ったディスプレイ基板の手前にボタンを配置する必要がある。
印刷後に組み立て式にするとなると、どこで分断して、どうやって繋ぎ合わせるのかということも考えなければいけない。
前提として、ねじを底面以外の外部に露出させるのは極力避けたい。
まずプラ板(アクリル板)挿入機構と基板部分を分けよう。ボディの分断を行う。
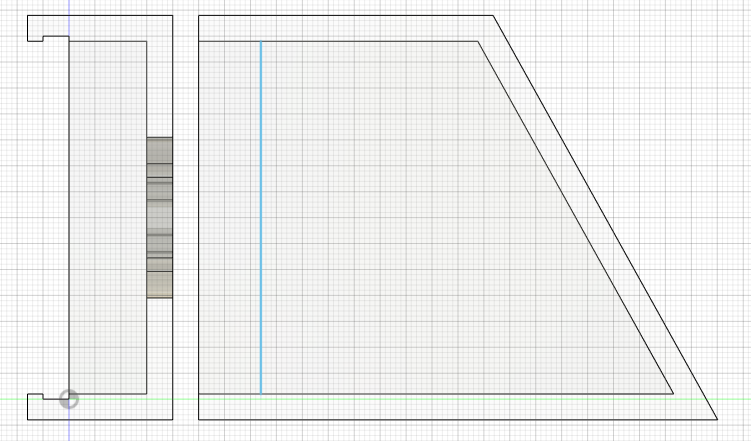
ぶった切った。15mm程内部の機構を隆起させる。
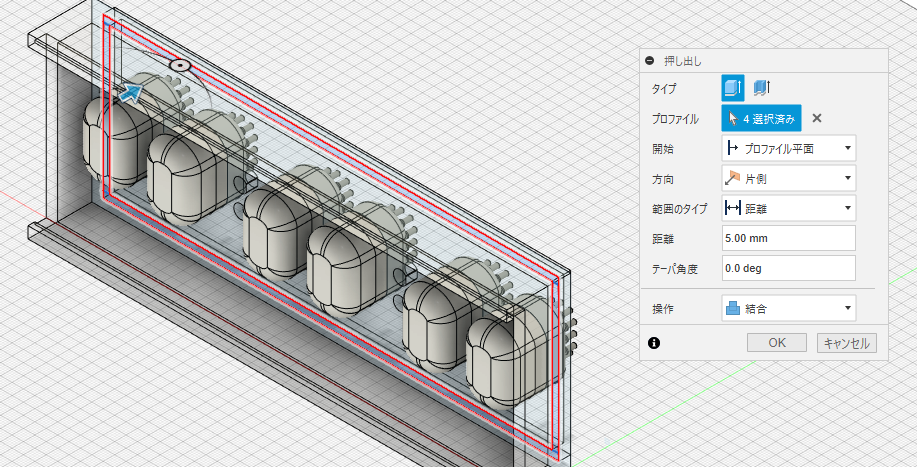
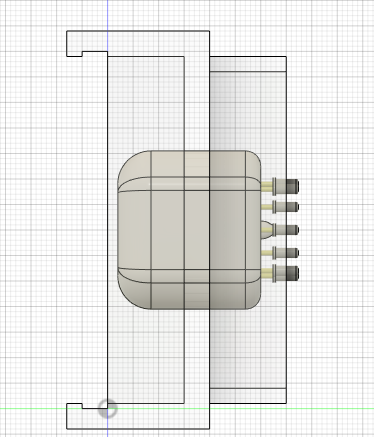
ボタン用の穴を作ろう。上面で丁度よさそうな場所の幅を測ると、190mmとなっていた。
ボタンは5個作りたいので、一つのボタンの長辺は190mm / 5 = 38mm となる。
とりあえず穴をあける。
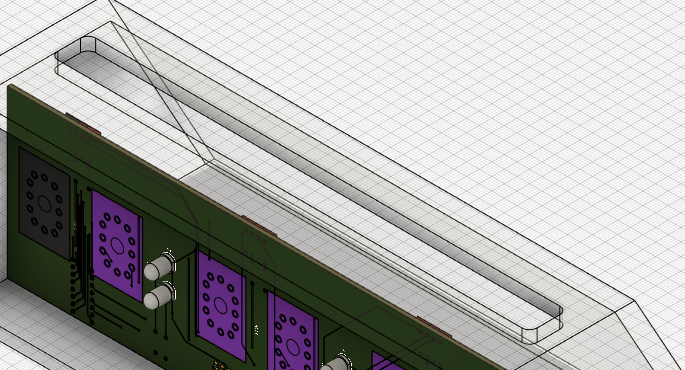
今後作る機能を考えると、密閉状態というのはよくない。通気口も作る。
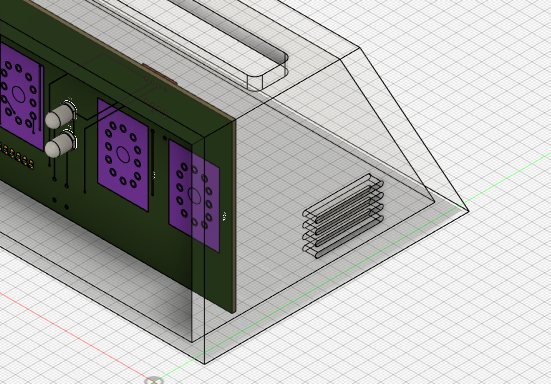
それっぽい穴が開いた。ではボタンの機構を考えよう。
考えている構造では、横並びのボタンというものは作れない。間に数ミリ程の区間を設ける。
そこの寸法は何mmにするか。バシッと、5mmにする。では、再計算するとどうなるか。
ボタンは5個、間のスペースは4箇所。これが5mmなので、190mm - 5mm × 4 = 170mm, 170mm / 5 = 34mm
つまりボタンの長辺は34mmだ。長辺34mmになるよう穴の一部をふさぐ。
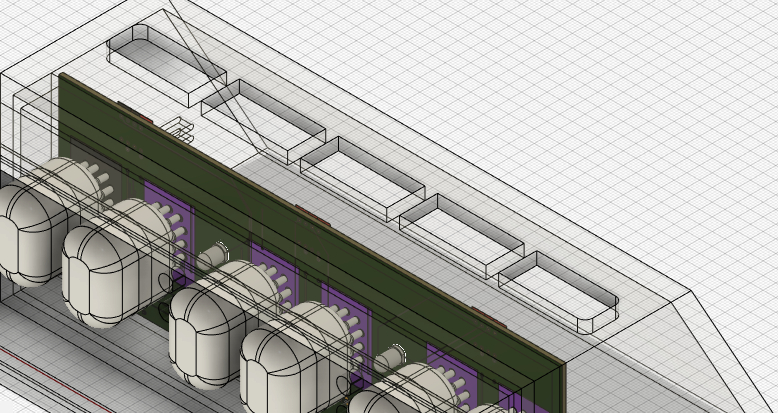
大分完成に見た目が近づいてきたようだ。ねじを使うとしたらどこなのか列挙する。
- 上面のボタン用基板の固定
- 電源・制御回路基板の固定
- 開閉式蓋部分の外装固定
ディスプレイ用基板部分は、電源・制御回路基板との接続とディスプレイ用外装に支えてもらうことにする。
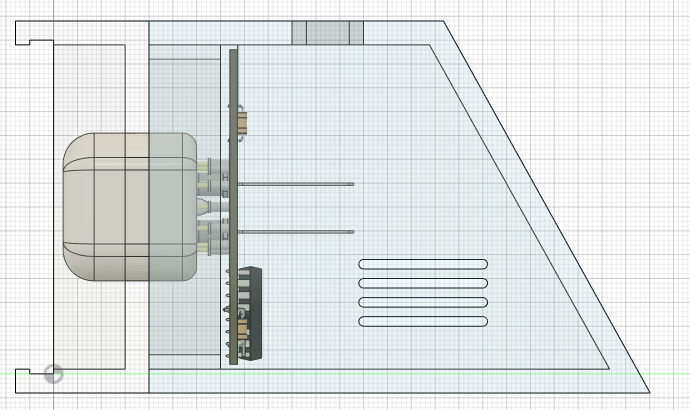
開く部分(蓋)と回路が入る筐体を分離しようとすると、また寸法の狂いを見つけた。また3:00を過ぎたのでここで終わりにする。また次回。